BLOG
Post Wire Inspection 101
The wire bond tech will keep on thriving in diverse areas of the electronic packaging industry, and its rapid growth won’t be limited to this era alone, it’ll also be predominant in the future.
Over the years, there have been some primary trends in this industry which have seen the inclusion of a constant increase in the quantity of circuit miniaturization, interconnections, the need for speed in the assembly process, and the reduction of cost for each connection.
Wirebonds machines have meticulously monitored this trend; these machines are very sophisticated, effective, quick, and dependable. But, there exist a minute problem which is that; wire bond inspection cannot automate inspection to certify the integrity of the wire-bond interconnections, which in one way or the other influences the quality of the finished product.
With an increase in the number of interconnections, comes an increase in the tendency of producing a defective component.
Since the wire bonding is often initiated at the end of the production, the cost of having a bad interconnection is usually great, compared to if the defect can be ascertained at the beginning of the process.
Thus, having a poor connection can significantly affect the cost and quality of the product.
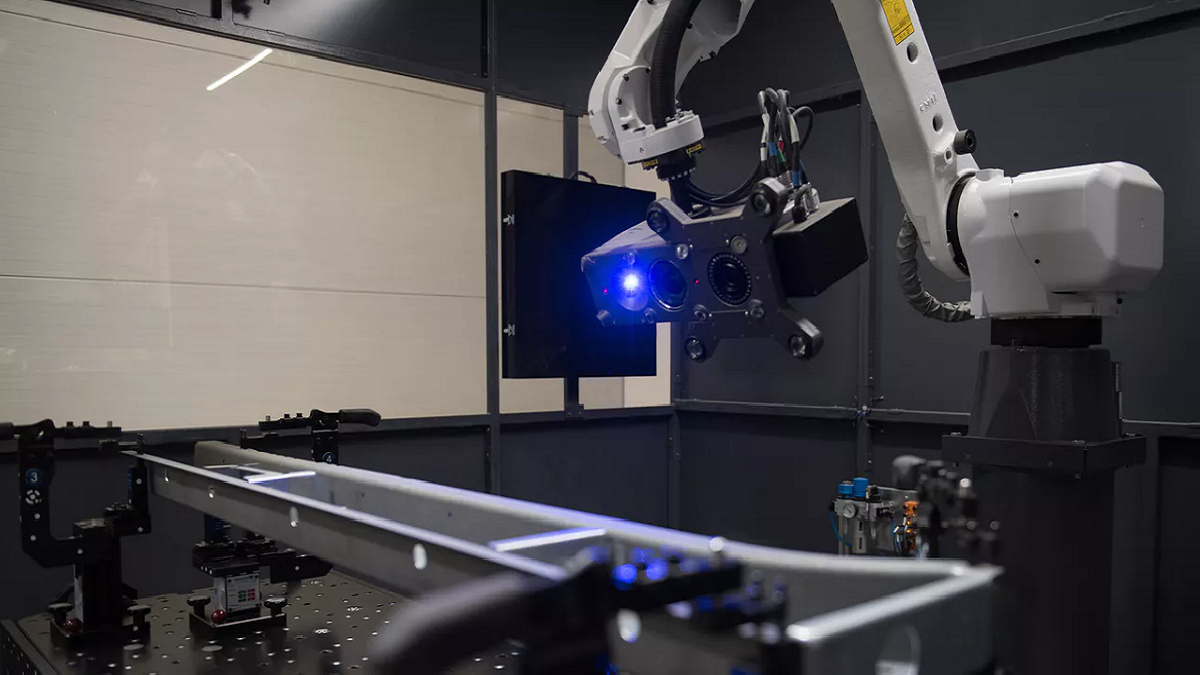
Nowadays, wire bond inspection is often carried out manually, visual check with the aid of a visual inspection system such as a microscope, contact inspection, or semi-automated inspection aided by an optical X-ray imaging sensor is utilized in this inspection process.
The inspection processes mentioned above are very costly, strenuous, and very slow. Because of the problems associated with the inspection process, they are always utilized to test the product on a sample basis.
The manual methods of wire bond inspection, that is, the visual and those aided by sensors, aren’t effective, and they often suffer from the inevitable dynamism of human inspection.
Because of the absence of automated measurements, they are subjective and often depend on the expertise of the operator.
Manual inspection puts the security of the wire to the test, using physical contact. This process isn’t fast enough, and it also comes with some risks like physical damage because of contact or potential electrostatic harm.
These methods are mainly restricted to wire-bond inspection, which can be viewed as another disadvantage. The capabilities of these inspection tools should cover the measurement of die placement and also check other components within the area of the wire bond for solder joint quality.
Today, we need to dig deep and discover a more effective, reliable, and faster means for inspection, which is versatile, capable of checking all wire-bond failure modes, measure-propelled, and very fast to keep up with production while busy inspecting all the products.
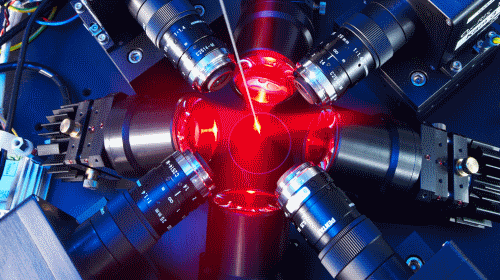
There is an effective inspection method that is available, and it is known as the rule-based automated optical inspection (AOI).
The AOI machine can effectively handle all measurement methods for all process steps in the PCB assembly.
The automated optical inspection is quite reliable in the inspection of solder paste, the placement of components, and the inspection of solder joints; it can also be used to reduce the cost associated with PCB assembly.
There are some popular advancements that have been carried out on AOI, and these advances are being propelled by certain improvements in camera technology and by the availability of some quick, reliable, and effective, economic computing systems.
Currently, the rule-based automated optical inspection adopts rapid and sensitive camera sensors, and several programmable LED illuminators propelled by complex algorithms for the inspection and measurement of wire bonds, and they can carry out this inspection in the best possible way without any defect or fault.
The result of its effectiveness is a higher inspection speed, and a reduced false accepts as well as rejects. The AOI is indeed the solution that we all have been waiting for, and it will be cool if efforts are made to unravel other solutions that can be seen as an upgrade of the AOI.
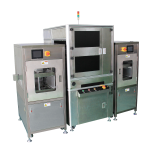
Contact Us
Cortex Robotics Sdn Bhd.
address
72-2-6, Arena Curve, Jalan Mahsuri,
11950 Bayan Lepas, Penang, Malaysia.
T: +604 – 611 0110
E: info@inspiren.dev
social media
quick link